標準にとらわれない
『NAKASAKU SOLUTIONS』。
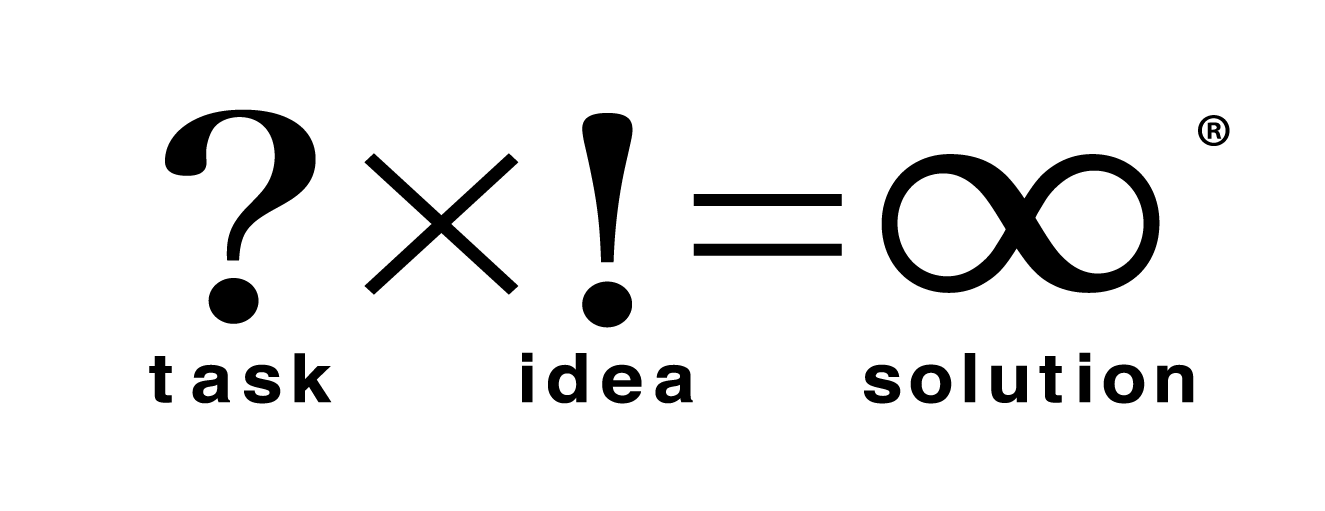
弊社のものづくりは、各部門担当者がユーザーのニーズをお伺いすることから始まります。
そして、次の4つの視点からユーザーにとって最良のご提案を行います。
① 無理のない理にかなった構成
② コストダウン
③ 制御と装置のコラボレーション
④ 使い勝手・メンテナンス
さまざまな業種のユーザーとの連帯で培ったノウハウ、”標準”にとらわれることない、弊社ならではのソリューション事例をご紹介します。
■ 搬送ラインを統合し、省スペースとコスト低減を実現
製品を並べたパレットを条件の整った順に4台ある乾燥炉のいずれかに投入し、製品を乾燥→取り出し→風冷冷却→取り出し→スタートのポジションへ返却する搬送ライン検討の依頼を頂きました。構想段階で投入ラインと返却ラインを統合することで省スペースとコスト低減が見込めたため、ユーザーに提案し、採用されました。統合するためには複雑な条件下で生産タクトの要求を満たす必要がありますが、各工程の制御条件を検証し、システムを構築することでその両方を実現しました。

■ 高度な裁断技術でコスト低減と品質向上を実現
ディスプレイや太陽光などのパネル製造現場では、フィルムやシート類の基材をカットシートで調達する場合が多く、かえって手間が掛かり非効率を生んでいました。そこで、原反ロールから必要な時に必要な枚数をカットできる装置の製作依頼を頂きました。樹脂シートは伸び縮みが激しい素材の性質上、切った長さを一定にコントロールするのが困難ですが、シートの長さがどのようになるかを予測して切断長さの誤差を小さくする高精度の制御によってコストを削減、また独自の裁断方法で切断面品質の向上を実現しました。
■ 設計製作の領域を超えて生産の仕組みを最適化
各企業の生産ノウハウを自動化するには、多くの場合は要求に合った汎用機がなく、通常は公開されていないため、参考になるものが見当たりません。まずは、ユーザーからのヒアリングを行い、仕様を決定し、コストバランスを考慮した最適な製造方法を検討していきます。そもそも、単純作業に思える手作業は、実は多くのことを同時に処理している場合があり、自動化するには様々な課題を乗り越える必要があります。
例えば、ファイルの金具を組み立てる装置では、以下のような課題がありました。
・どこまで自動化するかの切り分け
・パーツのNG品の振り分け、排出
・オペレーターの人員数の見直し
・生産タクトアップ
・既存の協力会社からの部品供給方法の見直し
・品質安定化のための剛性アップの検討
・設置スペースの制限による装置レイアウトの検討
弊社では、装置の設計製作の領域を超えて生産の仕組みを最適化する、システムインテグレーターとしてユーザーの課題に向き合います。
CONTACT お問い合わせフォーム
ご質問や資料請求など以下のフォームより問い合わせください